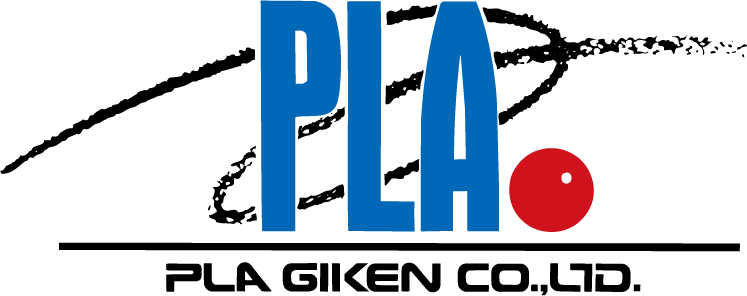
In extrusion devices for the medical field, we have numerous achievements: PVC sheet manufacturing equipment for blood bags and various manufacturing equipment for tube structures. In recent years, we have been particularly focusing on manufacturing equipment for catheter shafts and endoscope tubes.
Catheters for examinations and surgery need to be hard at the bottom but soft at the tip. Conventional manufacturing methods have so far involved connecting several jackets, each different in stiffness. However, in this method, there are uncertainties to the strengths of the jackets’ seams. In some cases, catheter fragmentation during surgery could leave some particles in the patient’s body. In order to develop a “seamless” catheter, we focused on a method of molding, where different resins are mixed together during extrusion.
At that time, in the field of plastic extrusion, mixing different resins was considered unconventional and difficult to achieve. This is because resins have different melting points depending on type, and viscosity changes according to temperature. The tasks of liquefying resins simultaneously and mixing them in a ratio changing over time added a further complication to the process control. After substantial trial & error, we devised Mixing Head, which is an extrusion head to that enables the production of catheter shafts with “variable durometer.”. Catheter shafts made using this new method have no “seams” between the jackets, which were inevitable in the conventional method. We were then able to register patents in Europe, the United States, China, Japan, and South Korea.